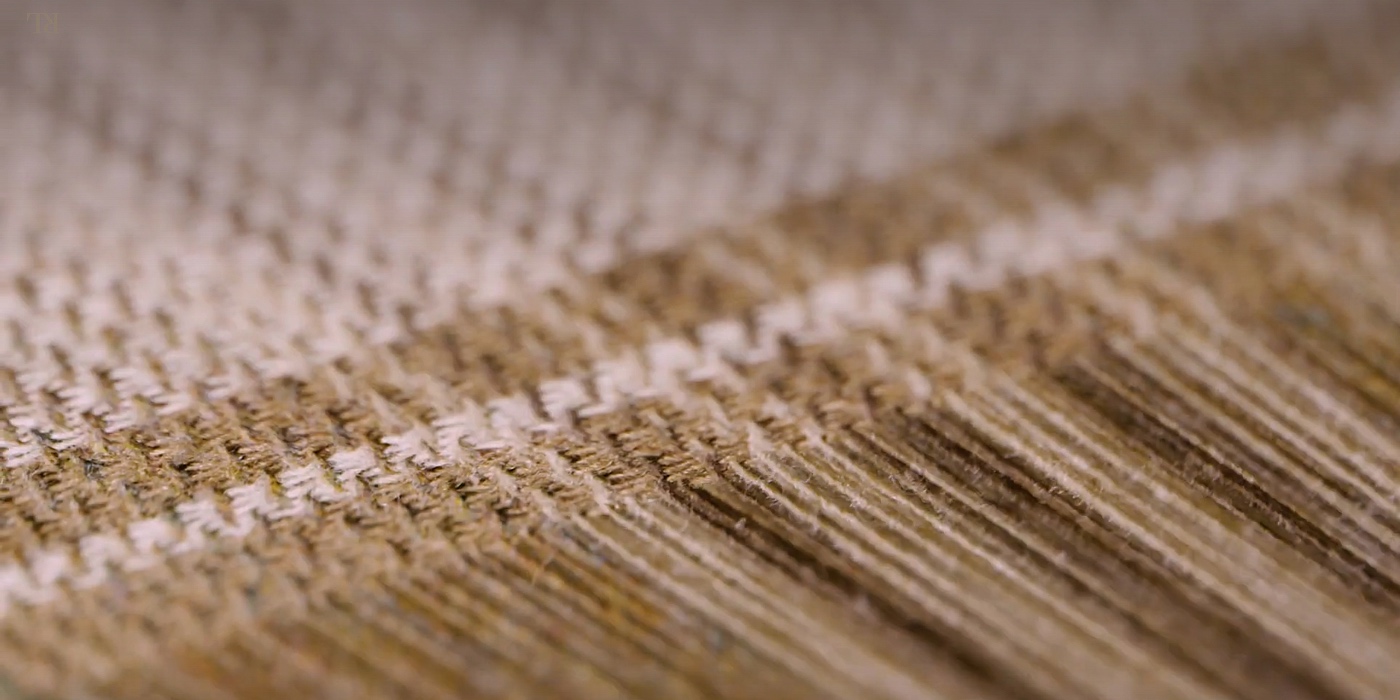
Cut From a Different Cloth
How three storied mills work with Ralph Lauren to create luxurious world of Purple LabelSimply put, there is no fabric more special than what you’ll find in Purple Label’s impeccably crafted suits. This isn’t hyperbole, it’s the result of a deliberate, methodical, and most of all unique process, one that sees Ralph Lauren working hand-in-hand with partner mills long before a single piece of fabric is born.
Unlike many brands, which choose so-called exclusive fabrics after the mill has spun them, Purple Label often requests, designs, and develops its fabrics before the mills begin weaving. It’s an elaborate, time-consuming way of working—one insider notes that the mills often do more development for Mr. Lauren than for their own collections—all to ensure that every Purple Label product embodies the ultimate in luxury and craftsmanship. It also guarantees that Purple Label’s Made to Measure customers receive a suit that doesn’t just fit to their exacting specifications but looks quite literally like no other suit in the world.
Here, the stories behind three of those mills, which happen to be among the world’s oldest and most revered.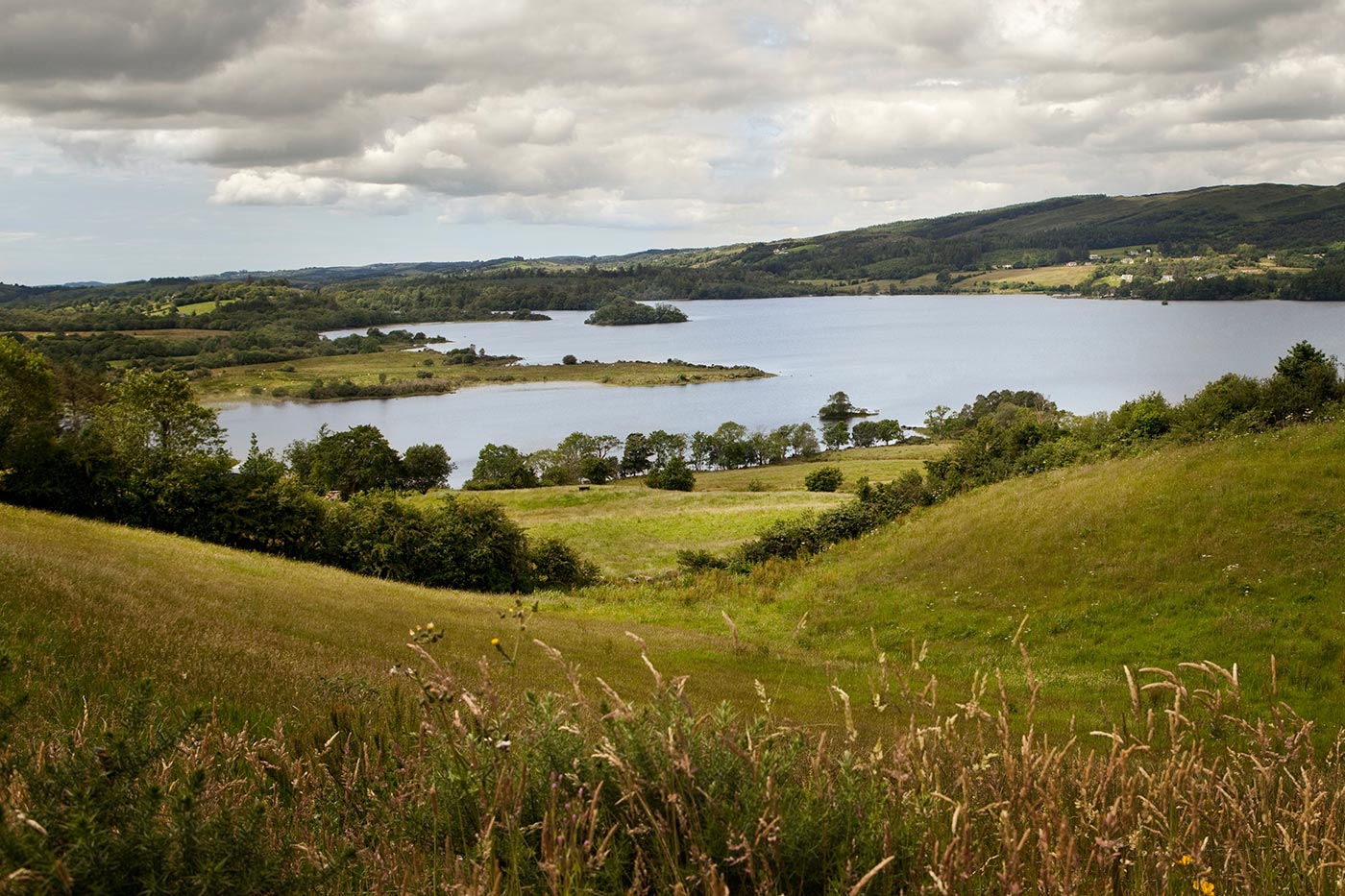
This Donegal, Ireland–based mill is inspiring to Mr. Lauren, and it’s easy to see why: Magee is one of the mills most associated with donegal tweed, which it has been producing for a century and a half, updating the traditional fabric with modern colors and textures, and lighter and softer materials. And yet some things have remained the same: The mill has had only two owners, the founder and namesake, John Magee, and then the Temple family, who bought the mill in 1910. They’ve partnered with Mr. Lauren for about 40 years, producing not just tweed but lambswool, Shetland, and alpaca, weaving some of the fabrics by hand in their facility next to the River Eske. Magee works hard to ensure that knowledge is passed down from generation to generation. “Natural fabrics require significant skill, time, and vocation to weave,” says Patrick Temple, CEO at Magee. “It takes between six to eight years to become a proficient weaver. The Magee team includes people with over 30 years of experience, who impart this to the younger members.” As that knowledge is passed down, there’s little doubt Magee will keep turning out top-flight tweed for another 150 years, at least.
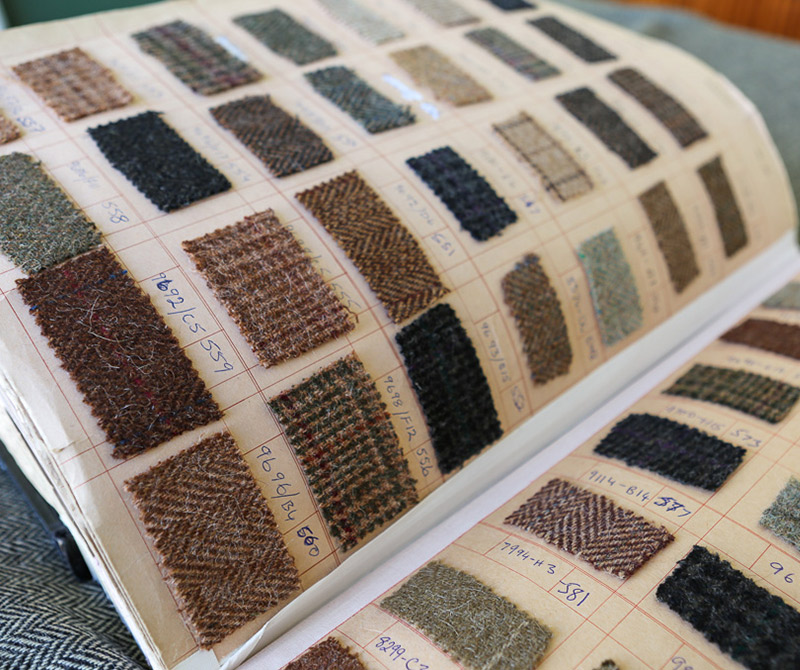
Holme Valley, in Huddersfield, West Yorkshire, has been a textile manufacturing hub since the 16th century. But, Bower Roebuck, like Magee 1866, is anything but stuck in the past. Bower specializes in worsted wool suiting, a field that has evolved over the years to keep up with changing tastes. Between global climate change, the advent of air conditioning, and the evolution of what men wear in the workplace, suits have become lighter and more comfortable—and Bower has kept pace, producing wools as light as 160 grams. (Experienced customers of fine suiting are familiar with the classification of wool known as Super 120s. Bower Roebuck was the first to produce it.) To do so, the mill has invested in cutting-edge looms and powerful computer equipment, combining such innovations with generations of experience to create some of the finest wools in the world. Mr. Lauren has worked with Bower Roebuck for nearly two decades, during which time the mill suffered through a massive flood, which closed its facility for six months. Bower smartly used the closure as an investment opportunity, returning with newer, more powerful equipment. But the closure was also a reminder not to take such storied mills for granted.
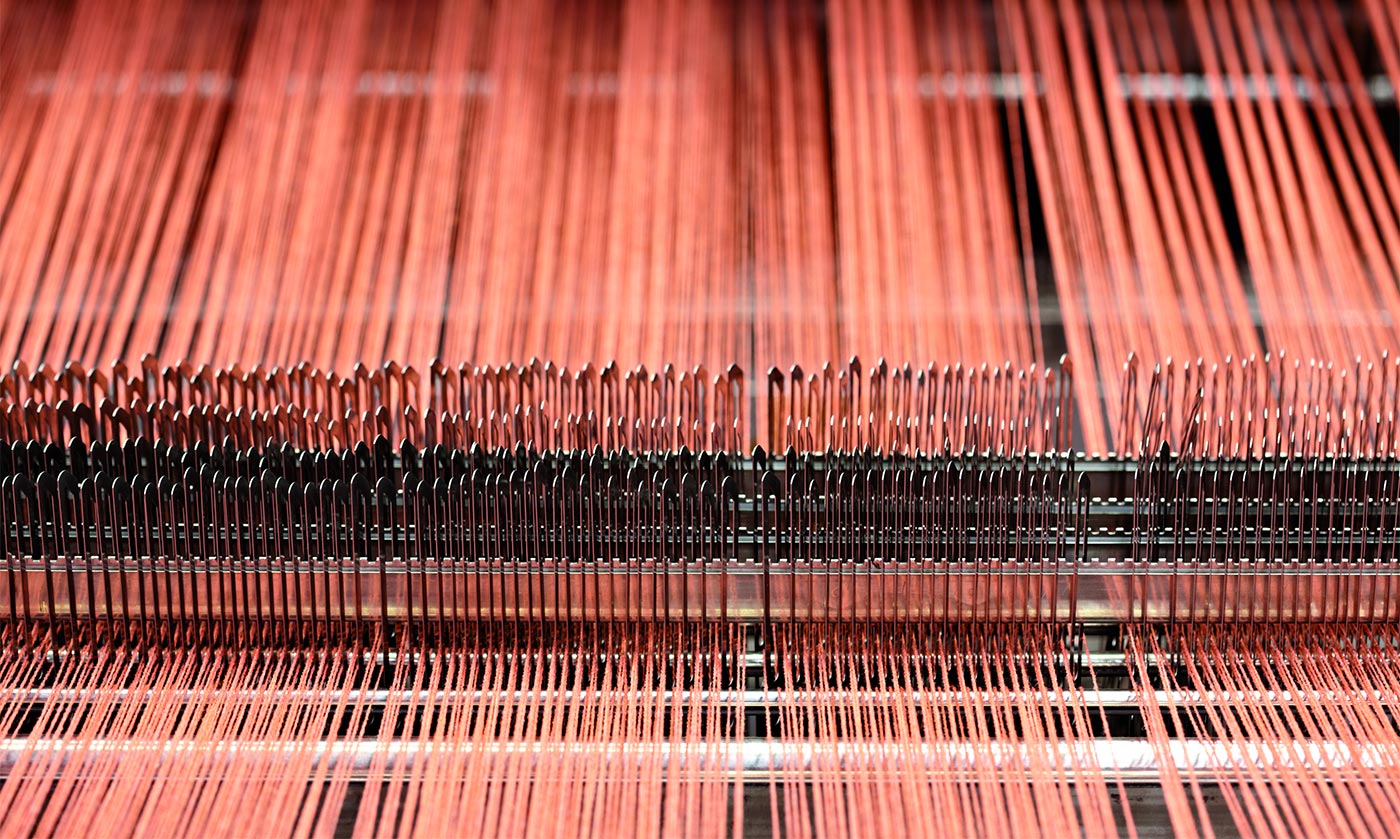
There is no finer cashmere than what is produced by this nearly 250-year-old mill in Yorkshire—one of the oldest cashmere mills in the UK. One key to producing such beautiful material is the in-house spinning, weaving, and finishing teams, which allow Ellis to innovate constantly, keeping up with Purple Label’s desire to introduce new fabrics almost every season—Kristie Reeves, sales and design director for Joshua Ellis, recalls that it took a year to get a particular lightweight fabric just right. (Joshua Ellis also provides luxurious textiles used in the Ralph Lauren Home collection.) Another key element: A shared sense of what looks good. “Our product fits Ralph’s aesthetic,” Reeves says. “The way that he envisions the brand fits hand in glove with our aesthetic.” Specifically, Reeves cites Mr. Lauren’s color preferences, sense of refinement, and his modern approach to heritage fabrics. “The way Ralph Lauren works is very unique,” she says. “The specificity of what’s needed, and working closely together so early in the process.” The resulting cashmere—used in Purple Label jackets, scarves, and more—speaks for itself.
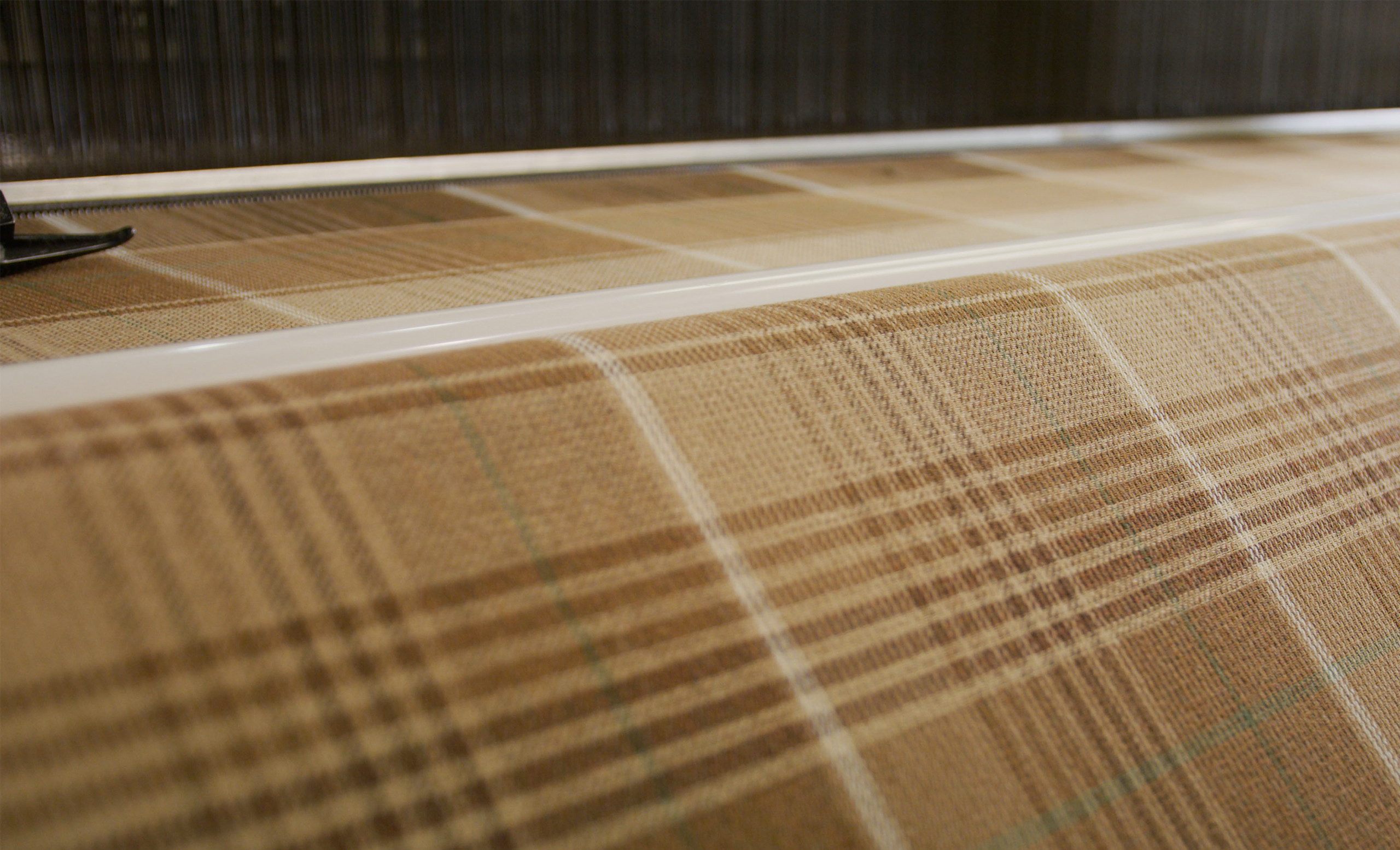
- Courtesy of Magee Mill
- Courtesy of Bower Roebuck
- Photograph BY MICHAEL WILLIAMS
- Courtesy of Joshua Ellis